What is the CCR reorganization process?
The continuous catalyst regeneration (CCR) reforming process is a key technology in the petroleum refining industry, especially for the production of high-octane gasoline. The process utilizes advanced catalysts, such as the PR-100 reforming catalyst, to convert low-octane naphtha into high-octane reformate, which is essential to meet the stringent requirements of modern gasoline formulations. In this article, we will explore the CCR reforming process, its significance, and the role of catalysts in improving gasoline quality.
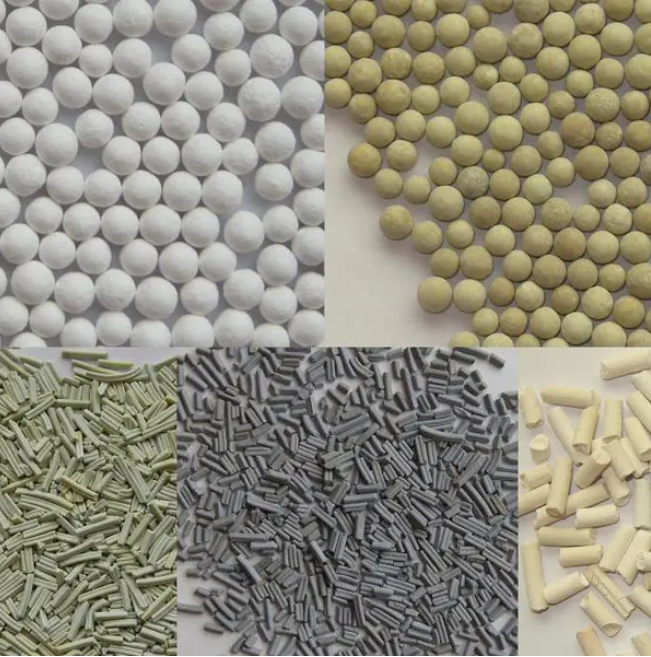
Understanding CCR Reform
CCR reforming is a continuously operating catalytic process that regenerates the catalyst while maintaining high production rates. The process is designed to increase the octane rating of naphtha, a key ingredient in gasoline production. A CCR reforming unit typically consists of a series of reactors where the naphtha is subjected to high temperatures and pressures in the presence of a catalyst.
The main reactions that occur during CCR reforming include dehydrogenation, isomerization, and cyclization. These reactions convert straight-chain hydrocarbons into branched hydrocarbons, which have a higher octane rating. The final product, reformate, is an important blending component for gasoline, providing the necessary octane boost to meet regulatory standards and consumer demand.
The role of PR-100 reforming catalyst
One of the most important advances in CCR reforming technology is the development of specialized catalysts, such as the PR-100 reforming catalyst. This catalyst is designed to increase the efficiency and selectivity of the reforming process. The PR-100 catalyst is characterized by high activity, good stability, and resistance to deactivation, which is essential to maintain optimal performance in continuous operation.
PR-100 catalyst promotes key reactions in the CCR reforming process, enabling the efficient conversion of naphtha into high-octane reformate. Its unique formulation and structure enable it to withstand the harsh conditions of the reforming environment, including high temperatures and the presence of impurities. As a result, PR-100 catalyst helps increase production and reduce operating costs, making it the preferred choice for many refineries.
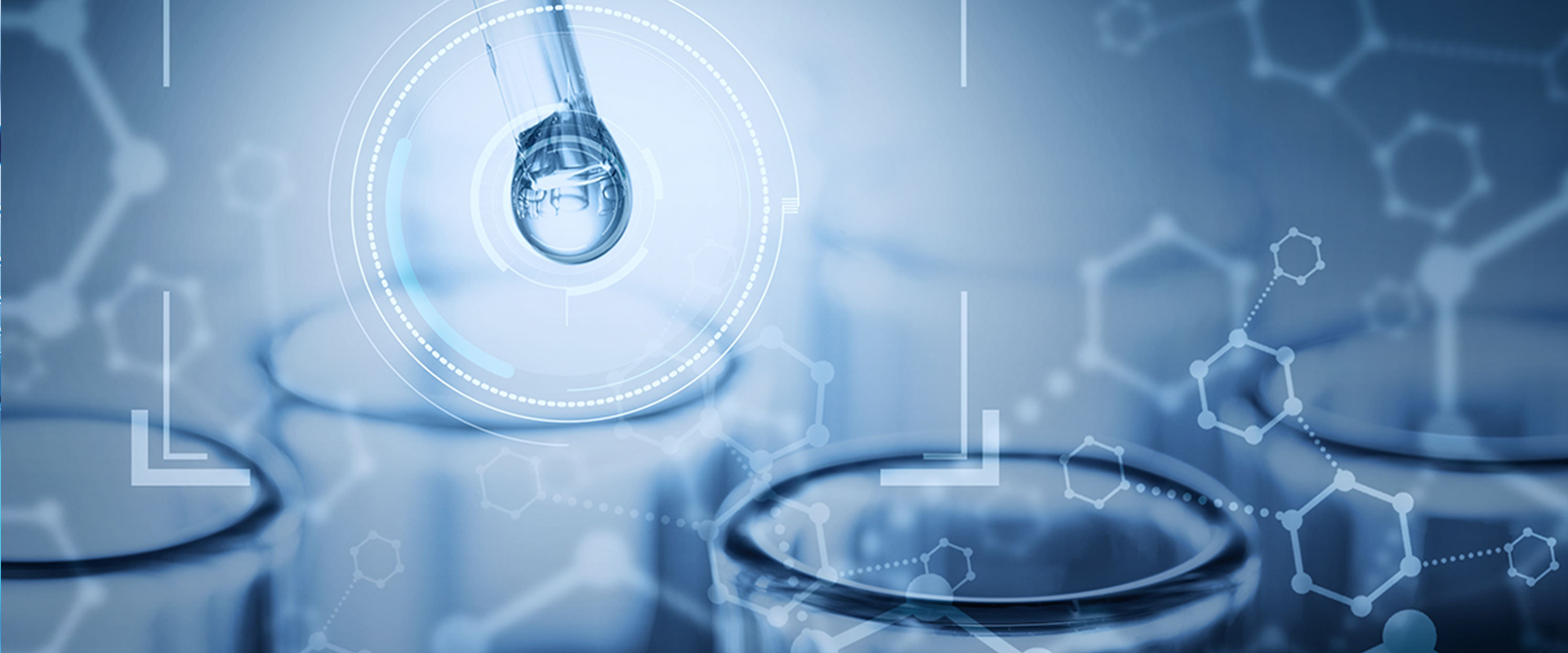
CCR reorganization process details
The CCR restructuring process can be divided into several key steps:
Feed Preparation: The naphtha feedstock is first treated to remove impurities such as sulfur and nitrogen compounds. This step is critical to prevent catalyst poisoning and ensure optimal performance.
Reforming reaction: The prepared naphtha is then fed into the reforming reactor, mixed with hydrogen and heated to high temperatures (usually between 500°C and 550°C). The presence of the PR-100 catalyst promotes the reforming reaction, converting the naphtha into high-octane hydrocarbons.
Catalyst Regeneration: A key feature of the CCR process is the ability to continuously regenerate the catalyst. When the catalyst loses activity due to carbon deposition (coking), the catalyst can be regenerated periodically by burning off the accumulated carbon in a controlled manner. This regeneration process keeps the catalyst active and extends its service life.
Product Separation: After the reforming reaction, the product mixture is cooled and sent to a separation unit where the reformate is separated from the unreacted naphtha and other by-products. The reformate is then further processed to meet gasoline specifications.
Hydrogen Recovery: The CCR reforming process also produces a large amount of hydrogen, which can be recovered and reused in the process or other applications in the refinery.
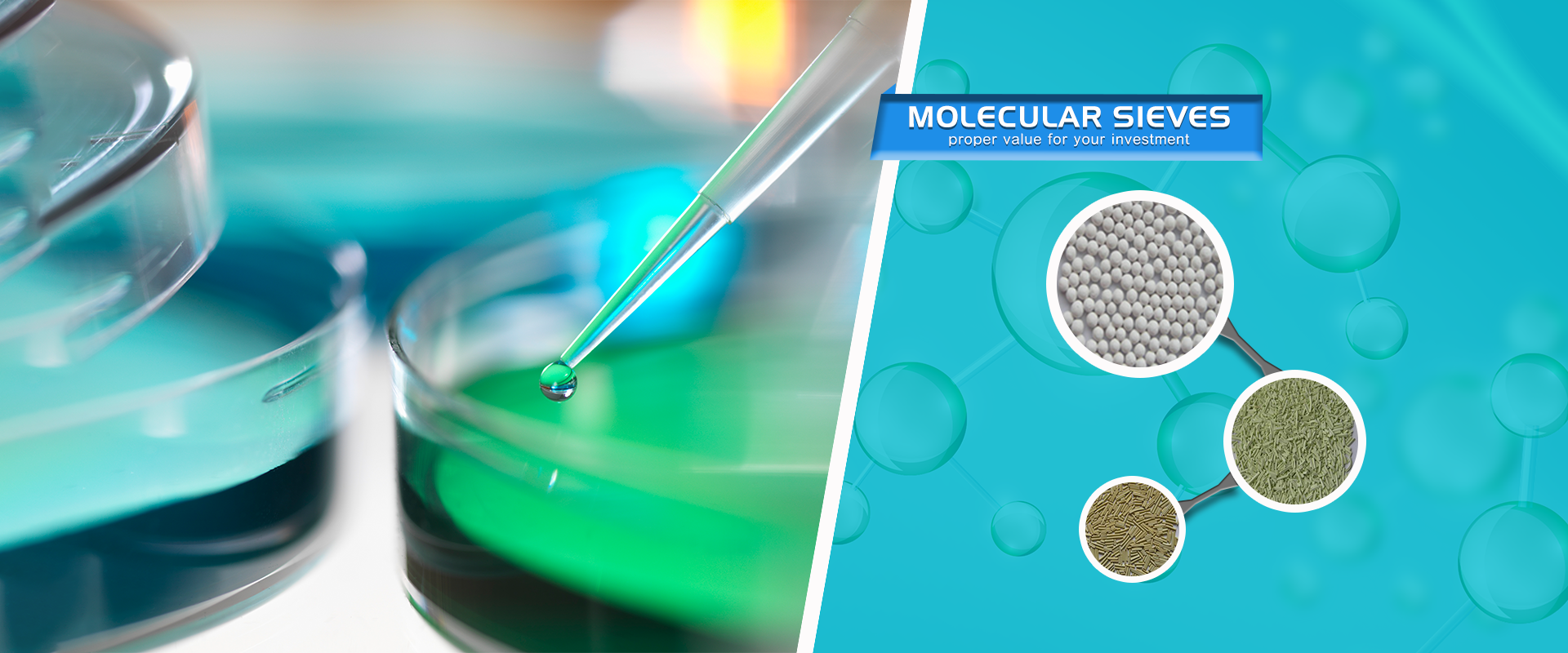
Advantages of CCR Restructuring
The CCR reforming process has the following advantages over traditional reforming methods:
Higher Yield: Continuous operation and efficient catalyst regeneration increase the yield of high-octane reformate products, thereby maximizing the value of the naphtha feedstock.
Increase octane: Using advanced catalysts such as PR-100 can produce reformate with higher octane numbers to meet the needs of modern gasoline formulations.
Operational flexibility: The CCR process can be easily integrated into existing refinery configurations, allowing flexibility to process different feedstocks and adjust to market demands.
Reduced Environmental Impact: By optimizing the reforming process and improving catalyst efficiency, refineries can reduce emissions, minimize waste, and achieve more sustainable operations.
in conclusion
The CCR reforming process is an important technology for producing high-octane gasoline, utilizing advanced catalysts such as PR-100 to improve efficiency and product quality. As the demand for cleaner, more efficient fuels continues to grow, the importance of CCR reforming in the petroleum refining industry will only grow. By understanding the intricacies of the process and the role of catalysts, refineries can optimize their operations and contribute to a more sustainable energy future.
Post time: Jan-21-2025