Catalytic reforming is a crucial process in the petroleum refining industry, primarily aimed at enhancing the quality of gasoline. Among the various reforming processes, Continuous Catalyst Regeneration (CCR) reforming stands out due to its efficiency and effectiveness in producing high-octane gasoline. A key component of this process is the reforming catalyst, which plays a vital role in facilitating the chemical reactions necessary for converting naphtha into valuable gasoline components.
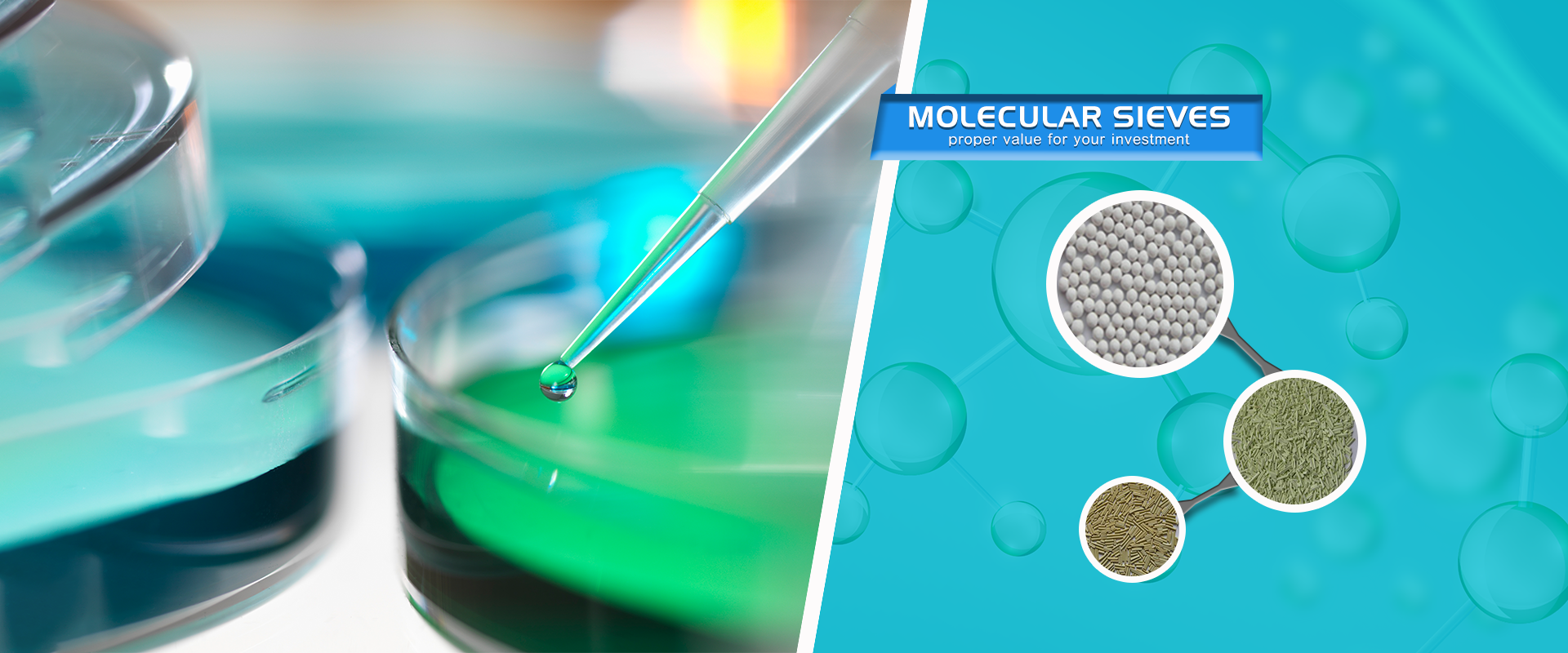
What is CCR Reforming?
CCR reforming is a modern refining technology that allows for the continuous regeneration of the catalyst used in the reforming process. This method contrasts with traditional batch reforming, where the catalyst is periodically removed for regeneration. In CCR reforming, the catalyst remains in the reactor, and the regeneration occurs in a separate unit, allowing for a more stable operation and higher throughput. This continuous process not only improves the yield of high-octane gasoline but also enhances the overall efficiency of the refining operation.
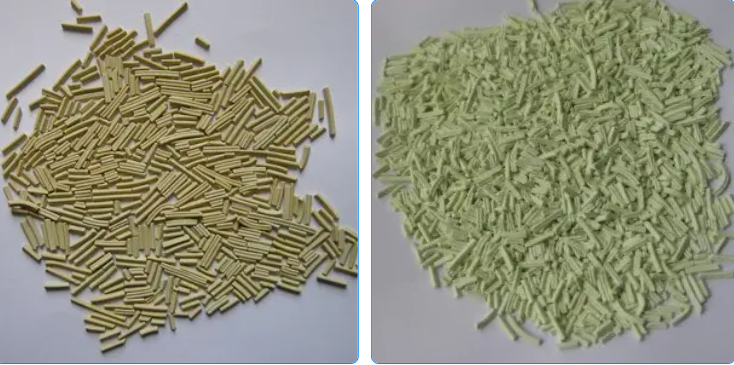
The Role of Catalysts in Reforming
Catalysts are substances that accelerate chemical reactions without being consumed in the process. In the context of CCR reforming, the catalyst is essential for several reactions, including dehydrogenation, isomerization, and hydrocracking. These reactions transform straight-chain hydrocarbons into branched-chain hydrocarbons, which have higher octane ratings and are more desirable in gasoline formulations.
The most commonly used catalysts in CCR reforming are platinum-based catalysts, often supported on alumina. Platinum is favored due to its excellent activity and selectivity in promoting the desired reactions. Additionally, the use of a bifunctional catalyst, which combines both metal and acid sites, allows for a more efficient conversion of naphtha into high-octane products. The metal sites facilitate dehydrogenation, while the acid sites promote isomerization and hydrocracking.
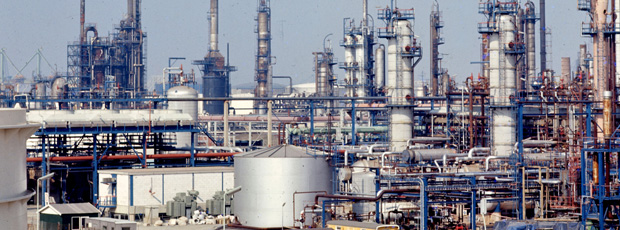
What Catalyst is Used in Reformer?
In CCR reforming, the primary catalyst used is typically a platinum-alumina catalyst. This catalyst is designed to withstand the harsh conditions of the reforming process, including high temperatures and pressures. The platinum component is responsible for the catalytic activity, while the alumina support provides structural stability and surface area for the reactions to occur.
In addition to platinum, other metals such as rhenium may be added to enhance the catalyst’s performance. Rhenium can improve the catalyst’s resistance to deactivation and increase the overall yield of high-octane gasoline. The formulation of the catalyst can vary depending on the specific requirements of the refining process and the desired product specifications.
Conclusion
Reforming catalysts, particularly in the context of CCR reforming, are integral to the production of high-quality gasoline. The choice of catalyst, typically a platinum-alumina formulation, significantly impacts the efficiency and effectiveness of the reforming process. As the demand for cleaner and more efficient fuels continues to rise, advancements in catalyst technology will play a pivotal role in shaping the future of gasoline production. Understanding the intricacies of these catalysts and their functions is essential for refining professionals aiming to optimize their operations and meet evolving market demands.
Post time: Oct-31-2024