Molecular sieves are essential materials for gas and liquid separation and purification in various industries. They are crystalline metalloaluminosilicates with uniform pores that selectively adsorb molecules based on their size and shape. The manufacturing process of molecular sieves involves several complex steps to ensure the production of high-quality materials with specific pore sizes and properties.
The production of molecular sieves starts with the selection of raw materials, including sodium silicate, alumina and water. These materials are mixed in precise proportions to form a homogeneous gel, which is then subjected to a hydrothermal synthesis process. In this step, the gel is heated to high temperatures in the presence of alkaline substances to promote the formation of a crystal structure with uniform pores.
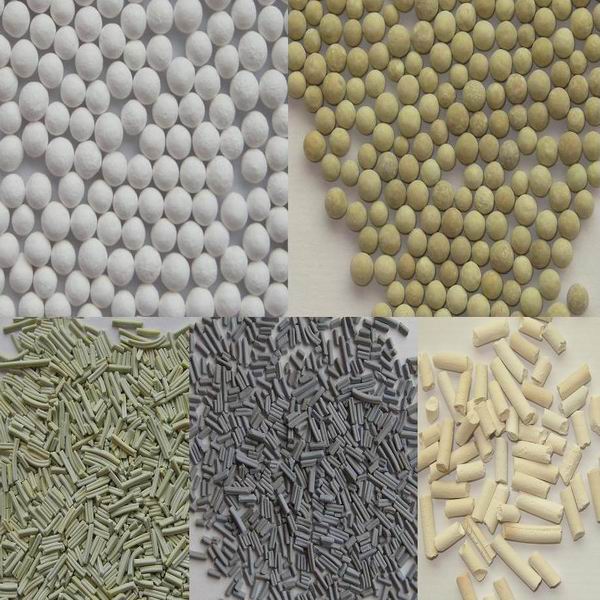
The next critical stage in the manufacturing process is ion exchange, which involves replacing sodium ions in the crystal structure with other cations such as calcium, potassium or magnesium. This ion exchange process is critical for regulating the performance of molecular sieves, including adsorption capacity and selectivity. The type of cation used for ion exchange depends on the specific application requirements of the molecular sieve.
After ion exchange, the molecular sieves undergo a series of washing and drying steps to remove any impurities and residual chemicals from the production process. This ensures that the final product meets the stringent purity standards required for industrial applications. After the washing and drying process is complete, the molecular sieves are calcined at high temperatures to stabilize the crystal structure and remove any remaining organic compounds.
The final step in the manufacturing process involves activation of the molecular sieves to prepare them for adsorption applications. This activation process typically involves heating the molecular sieve at high temperatures to remove moisture and enhance its adsorption properties. The duration and temperature of the activation process are carefully controlled to achieve the desired pore size and surface area of the molecular sieve.
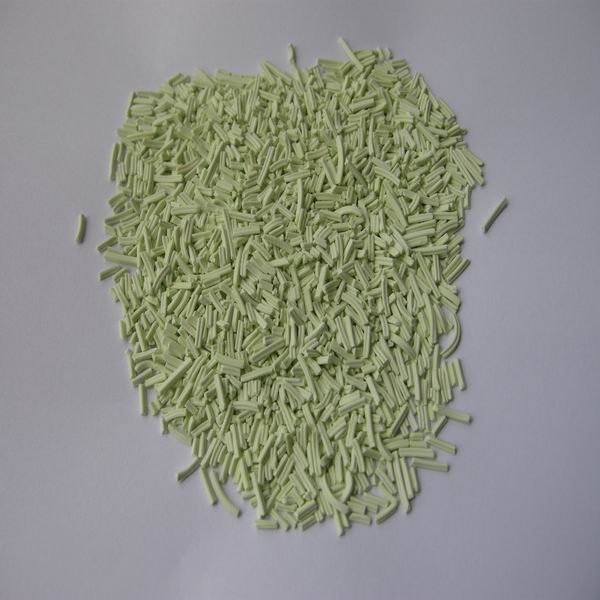
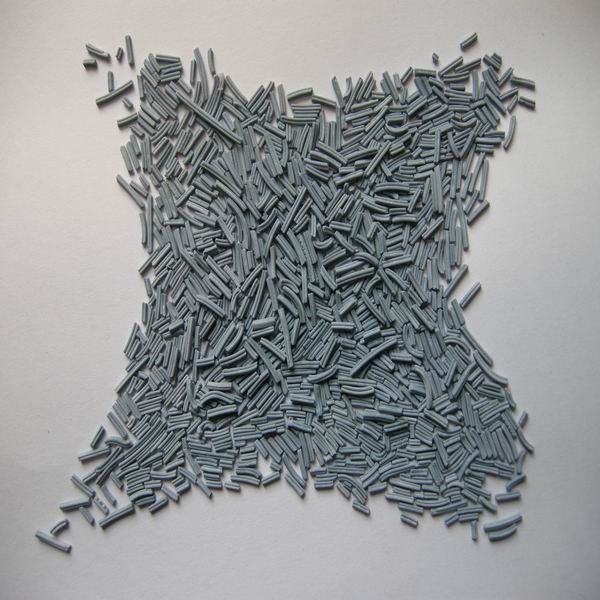
Molecular sieves are available in different pore sizes, including 3A, 4A and 5A, each suitable for specific applications. For example, 3A molecular sieves are often used for dehydration of gases and liquids, while 4A and 5A molecular sieves are preferred for adsorbing larger molecules and removing impurities such as water and carbon dioxide.
In summary, the manufacturing of molecular sieves is a complex and sophisticated process involving several key steps, including hydrothermal synthesis, ion exchange, washing, drying, calcination, and activation. These steps are carefully controlled to produce molecular sieves with customized properties and pore sizes to meet the diverse needs of industries such as petrochemical, pharmaceutical and natural gas processing. High-quality molecular sieves manufactured by reputable manufacturers play a vital role in achieving efficient separation and purification processes in various industrial applications.
Post time: Apr-19-2024